
We are a PLASTIC INJECTION MOLDING COMPANY SERVING St. LOUIS.
Unleash the potential of plastic with ASH INDUSTRIES' precision injection molding expertise.
We transform raw plastic pellets into high-quality, complex parts through a streamlined plastic injection molding process.
We utilize cutting-edge technology to deliver durable, consistent parts for any application, bringing your plastic visions to life.
We aren't just making injection molded parts, we're crafting excellence. Our commitment to cutting-edge technology, high-quality materials, and meticulous processes ensures we deliver the best possible results for your project.
Need a complex geometry?
Extra strength? New material?
ASH knows how to translate your needs into deliverables.
Exceptional injection molded parts come from smarter thinking.
Unleash the potential of plastic with ASH INDUSTRIES' precision injection molding expertise serving all of the St. Louis to Belleville, Springfield, to Columbia and Kansas City areas.
As Plastic Injection molders, we transform raw plastic pellets into high-quality, complex parts through a streamlined Plastic Injection Molding process
We aren't just making injection molded parts, we're crafting excellence. Our commitment to cutting-edge technology, high-quality materials, and meticulous processes ensures we deliver the best possible results for your project.
Need a complex geometry?
Extra strength? New material?
ASH knows how to translate your needs into deliverables.
Exceptional injection molded parts come from smarter thinking.
WE LIKE CHALLENGES
That's our story at ASH INDUSTRIES. We're a team of real engineers, not just salespeople, and we specialize in molding the tough parts.
NEED A PLASTIC INJECTION MOLDER?
WATCH THE VIDEOS to see everything you need from St. Louis to Belleville, Springfield, to Columbia and Kansas City for plastic injection molding suppliers near you!
Unleash the potential of plastic with ASH INDUSTRIES' precision injection molding expertise serving all of the St. Louis to Belleville, Springfield, to Columbia and Kansas City areas.
As Plastic Injection molders, we transform raw plastic pellets into high-quality, complex parts through a streamlined Plastic Injection Molding process.
We utilize cutting-edge technology to deliver durable, consistent parts for any application, bringing your plastic visions to life.
We aren't just making injection molded parts, we're crafting excellence. Our commitment to cutting-edge technology, high-quality materials, and meticulous processes ensures we deliver the best possible results for your project.
Need a complex geometry?
Extra strength? New material?
ASH knows how to translate your needs into deliverables.
Exceptional injection molded parts come from smarter thinking.
Challenge-
That's our story at ASH INDUSTRIES. We're a team of real engineers, not just salespeople, and we specialize in molding the tough parts.
WE LIKE CHALLENGES
That's our story at ASH INDUSTRIES. We're a team of real engineers, not just salespeople, and we specialize in molding the tough parts.
MEDICAL MOLDING
ASH offers unparalleled medical molding capabilities with our state-of-the-art, ISO Class 7 clean room. This controlled environment minimizes airborne particles and contaminants, ensuring your medical components are manufactured to the strictest standards.
This meticulous approach safeguards the integrity of your parts, fostering patient safety and regulatory compliance.
Trust us to deliver medical-grade plastic parts with unmatched quality and precision.

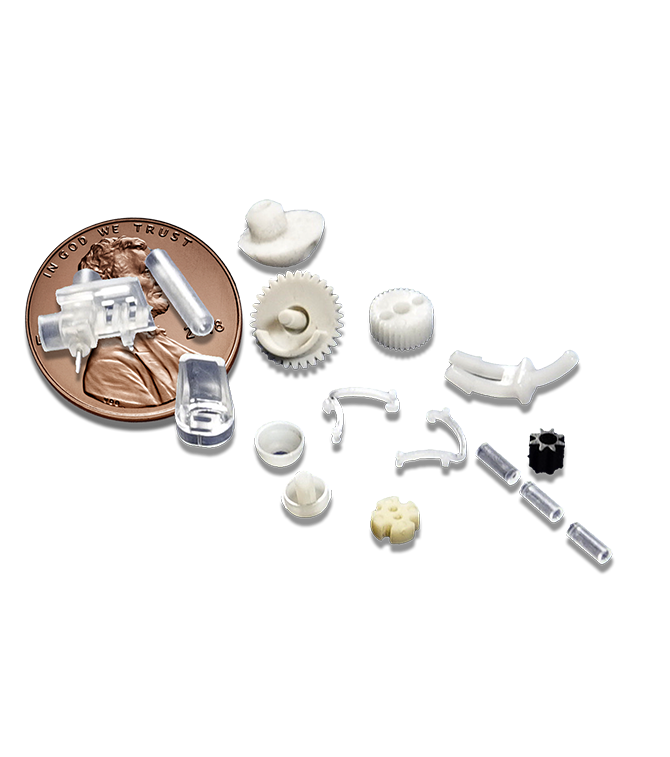
MEDICAL MOLDING
ASH offers unparalleled medical molding capabilities with our state-of-the-art, ISO Class 7 clean room. This controlled environment minimizes airborne particles and contaminants, ensuring your medical components are manufactured to the strictest standards.

OVERMOLDING
Push the boundaries of plastic parts with our innovative overmolding process.
This advanced technique takes your injection molded base and seamlessly combines it with a second material, often a soft, rubber-like TPE. This creates a single part with a unique blend of properties. Imagine ergonomic grips for enhanced user comfort, decorative finishes for a touch of style, or even improved functionality like water resistance.
Overmolding opens a world of possibilities, allowing you to tailor your parts for superior performance, ergonomics and aesthetics.
FIREARMS
We understand the demands of firearm components. At ASH INDUSTRIES, we utilize high-precision injection molding to deliver parts known for their strength, reliability, and dimensional accuracy. Our commitment to quality ensures each component performs flawlessly, meeting the expectations of both manufacturers and firearm enthusiasts.
MEDICAL DEVICES
Overmolding Improves grip and control for surgical instruments like scalpels, forceps, and other instruments. Overmolding also works on hand held devices like nebulizers or blood pressure monitors. If you need enhanced durability and protection for delicate internal components of medical devices like defibrillators or anesthesia machines from impact and external factors. Luer fittings and other connectors benefit from overmolds that create secure seals to prevent leaks of fluids or gases.
Biocompatibility is improved with overmolding for implants that integrate with the body.
watch these videos

We are a PLASTIC INJECTION MOLDING COMPANY SERVING St. LOUIS to Kansas City

We are a PLASTIC INJECTION MOLDING COMPANY SERVING ST. LOUIS

TUNGSTEN INFUSED THERMOPLASTIC ELASTOMER PARTS
Take your thermoplastic parts to the next level with tungsten infusion. This innovative process increases specific gravity with tungsten particles, creating components that are incredibly dense, durable, and resistant to wear but have the weight you might need for a surgical instrument or firearms frame, grips, or components.
Get all the properties of engineering grade thermoplastic with added weight and feel. Tungsten-infused molding pushes the boundaries of what's possible.
TUNGSTEN INFUSED THERMOPLASTIC ELASTOMER PARTS
Take your thermoplastic parts to the next level with tungsten infusion. This innovative process increases specific gravity with tungsten particles, creating components that are incredibly dense, durable and resistant to wear but have the weight you might need for a surgical instrument or firearm frame, grip, or components.
Get all the properties of engineering grade thermoplastic with added weight and feel. Tungsten-infused molding pushes the boundaries of what's possible.

35 TON to 850 TON
Single or Multi Cavity



1
STARTING RIGHT!
DESIGN for MANUFACTURING
Optimizing Your Plastic Parts Digitally
Design for Manufacturability (DFM) is your secret weapon for transforming innovative concepts into production-ready roto-molded parts. By collaborating with our DFM experts early on, you can identify potential manufacturing roadblocks. We'll point out potential design-driven challenges and suggest adjustments that optimize your design for efficient molding, minimizing waste and production costs. This ensures your functional parts are also manufacturable, saving you time and money while bringing your vision to life.
-
Reduced Production Costs: Streamlined designs minimize material waste, optimize cycle times, and simplify the molding process, leading to lower production costs.
-
Enhanced Quality: DFM helps identify potential design-driven molding defects like sink marks, warping, or hard to fill areas, ensuring your parts meet the highest quality standards.
-
Faster Time to Market: By identifying potential issues upfront, DFM allows for a smoother transition from design to production, accelerating your time to market.

1
IT STARTS WITH DESIGN
DESIGN for MANUFACTURING
Optimizing Your Plastic Parts Digitally
Design for Manufacturability (DFM) is your secret weapon for transforming innovative concepts into production-ready roto-molded parts. By collaborating with our DFM experts early on, you can identify potential manufacturing roadblocks. We'll point out potential design-driven challenges and suggest adjustments that optimize your design for efficient molding, minimizing waste and production costs. This ensures your functional parts are also manufacturable, saving you time and money while bringing your vision to life.
-
Reduced Production Costs: Streamlined designs minimize material waste, optimize cycle times, and simplify the molding process, leading to lower production costs.
-
Enhanced Quality: DFM helps avoid common molding defects like sink marks, warping, or short shots, ensuring your parts meet the highest quality standards.
-
Faster Time to Market: By identifying potential issues upfront, DFM allows for a smoother transition from design to production, accelerating your time to market.

MOLD CONTROL
WHY YOU NEED AN IN-HOUSE TOOLROOM
THE MOST IMPORTANT PART OF THE PROCESS
In-house mold building is a game-changer for injection molding. Imagine seamless communication between design and toolmakers, speeding up development and getting your product to market faster. Direct control over quality ensures molds meet your exact specs, reducing defects. In-house tooling keeps everything streamlined, potentially saving costs. It's a strategic advantage for any serious molding company.
2



WHERE TO BUILD THE MOLD?
2

THE MOST IMPORTANT PART OF THE PROCESS
In-house mold building is a game-changer for injection molding. Imagine seamless communication between design and toolmakers, speeding up development and getting your product to market faster. Direct control over quality ensures molds meet your exact specs, reducing defects. In-house tooling keeps everything streamlined, potentially saving costs. It's a strategic advantage for any serious molding company.
YOUR MOLD & IN-HOUSE TOOLROOM



GET THE BALL ROLLING
Maybe you don't know which process to use, so let us help with a free engineering consult.
This is where you get great ideas
The earlier you get your supplier involved, the better chance that you will save something big. It could be time, money, functionality or even a new idea.
We specialize in the "tough challenges", the projects that need extra attention, experimentation or a new material. There's no better molding company than ASH to do this.
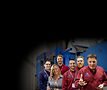
GET THE BALL ROLLING
Maybe you don't know which process to use, so let us help with a free engineering consult.
This is where you get great ideas
The earlier you get your supplier involved, the better chance that you will save something big. It could be time, money, functionality or even a new idea.
We specialize in the "tough challenges", the projects that need extra attention, experimentation or a new material. There's no better molding company than ASH to do this.



GET THE BALL ROLLING
Maybe you don't know which process to use, so let us help with a free engineering consult.
This is where you get great ideas
The earlier you get your supplier involved, the better chance that you will save something big. It could be time, money, functionality or even a new idea.
We specialize in the "tough challenges", the projects that need extra attention, experimentation or a new material. There's no better molding company than ASH to do this.

ASH FACTS:
-
Thermoplastic Injection Molding
-
Rotomolding
-
Tool & Die manufacturing
-
Silicone Molding
-
3D Printing Production
-
Design for Manufacturing (DFM)
-
Low volume 3D production
-
3D Plastic Printing
-
Metal Injection Molding
-
Yes, ASH can help you manufacture your parts in low volume. We can even 3D print your first prototypes. When you want to have less than 1000 but don't want to pay for full production runs we have a flat rate low volume program called SUPERMOLD. This can have many benefits, including a faster time to market and a low initial investment but still allow you to produce high-quality parts.
Of course NDA's are necessary to protect your IP. We value privacy and confidentiality and that is one of your main reasons for making parts in the USA. NDA's are enforceable here unlike sourcing overseas. Confidentiality is one of the most important factors in choosing a new molding supplier.
We are ISO 9001 compliant and ISO 13485 with a ISO Class 7 medical cleanroom.
Yes we do, besides our founder graduating from Massachusetts Institute of Technology with a degree in 6-1, Electrical Engineering-Hardware, we also have a biomedical engineer, mechanical engineers and other manufacturing engineers on staff to help you think smarter to save money.

People also ask:
Injection molding is a manufacturing process where liquid plastic is injected under high pressure into a mold cavity. This cavity is shaped like the final desired part, and once the plastic cools and hardens, the finished part is ejected. This technique allows for mass production of complex and precise plastic parts.
The SUPERMOLD program utilizes specialized inserts for existing molds, so we simply machine a small area to make your sample parts in that time frame, The lifetime tooling is then ready for full production runs very quickly.
SuperMolds are extremely cost effective with prices beginning at $4900 for what would often cost $12000 or more at other facilities. That's why the ASH SUPERMOLD PROGRAM is so economical. Even larger, more complex molds will be cost effective when ASH offers a plan to build the tooling.
An alternative plastic manufacturing process could be thermoforming, CNC machining, thermoset compression molding, blow molding, or 3D printing. These options offer various pros and cons, but some can be viable depending on your part size and complexity
SuperMolds have a lifetime warranty, but even normal injection molds are carefully maintained by ASH’s in-house tool-making facility. Typical plastic injection molds last from hundreds of thousands to over a million cycles but here, a plastic injection mold lifespan is extended to the extreme thanks to our maintenance, structure, SPI classification, and materials.
The scrap produced from the injection molding process can be recycled back into the manufacturing process, post-industrial scrap can be shred and fed back into the injection molding machine or the plastic melted into pellets for reuse. No turtles are harmed from an injection molding plant.
The cumulative cost of 3D printing can be staggering. Piece-part price for injection molding is going to be significantly lower compared to 3D printing once you reach a high volume of parts. By utilizing SuperMold to minimize capital investment, the smart point to switch from 3D printing to injection molding occurs much sooner.
People also ask:
Injection molding is a manufacturing process where liquid plastic is injected under high pressure into a mold cavity. This cavity is shaped like the final desired part, and once the plastic cools and hardens, the finished part is ejected. This technique allows for mass production of complex and precise plastic parts.
The SUPERMOLD program utilizes specialized inserts for existing molds, so we simply machine a small area to make your sample parts in that time frame. The lifetime tooling is then ready for full production runs very quickly.
SuperMolds are extremely cost effective with prices beginning at $4900 for what would often cost $12000 or more at other facilities. That's why the ASH SUPERMOLD PROGRAM is so economical. Even larger, more complex molds will be cost effective when ASH offers a plan to build the tooling.
An alternative plastic manufacturing process could be thermoforming, CNC machining, thermoset compression molding, blow molding, or 3D printing. These options offer various pros and cons, but some can be viable depending on your part size and complexity
SuperMolds have a lifetime warranty, but even normal injection molds are carefully maintained by ASH’s in-house tool-making facility. Typical plastic injection molds last from hundreds of thousands to over a million cycles but here, a plastic injection mold lifespan is extended to the extreme thanks to our maintenance, structure, SPI classification, and materials.
The scrap produced from the injection molding process can be recycled back into the manufacturing process, post-industrial scrap can be shred and fed back into the injection molding machine or the plastic melted into pellets for reuse.
The cumulative cost of 3D printing can be staggering. Piece-part price for injection molding is going to be significantly lower compared to 3D printing once you reach a high volume of parts. By utilizing SuperMold to minimize capital investment, the smart point to switch from 3D printing to injection molding occurs much sooner.
Choosing the right injection molding company for your custom parts is crucial for success.
Here are some key factors in choosing an injection molding supplier:
Experience and Capabilities:
-
Expertise in your industry: Look for a company with experience in producing parts similar to yours. This ensures they understand the specific requirements and challenges of your application.
-
Capability for your part complexity: Can they handle the level of detail and precision your parts require? Consider factors like wall thickness, tight tolerances, and intricate features.
-
Variety of materials offered: Do they have experience with the materials you need for your parts? Do they have the proper equipment to handle, monitor, and process specialized material. This could include engineering resins or high performance materials.
Quality and Process Control:
-
Commitment to quality: Look for a company with a strong quality management system and certifications like ISO 9001. This indicates their commitment to consistent quality control throughout the manufacturing process.
-
Inspection capabilities: Do they have the necessary equipment and expertise to inspect your parts for dimensional accuracy, surface finish, and any potential defects?
-
Process control practices: Inquire about their approach to monitoring and maintaining consistent molding parameters for your parts.
Communication and Customer Service:
-
Responsiveness and communication style: Choose a company that is easy to communicate with and understands your needs. They should be able to answer your questions clearly and keep you informed throughout the process.
-
Project management: Do they have a dedicated project manager who will oversee your project from start to finish? This ensures clear communication and timely updates.
-
Customer service philosophy: Look for a company that prioritizes customer satisfaction and is willing to work collaboratively to achieve your desired outcome.
Pricing and Production Capacity:
-
Competitive pricing: Get quotes from several companies to compare pricing structures. Consider whether they offer upfront tooling costs or per-unit pricing. What creative solutions do they offer to finance and launch a new product and tooling?
-
Production capacity: Can they meet your production volume requirements and deliver your parts within your desired time frame?
-
Lead times: Understand the typical lead times for mold development, part production, and any potential lead time variations depending on order volume.
Additional Considerations:
-
Education: How well are they educating you on how your project will progress.
-
Sustainability practices: If environmentally conscious manufacturing is a priority for you, inquire about the company's sustainability practices and material recycling programs.
-
By carefully evaluating these factors, you can select an injection molding company that possesses the expertise, quality standards, and customer focus to deliver the best possible results for your custom parts.

